三坐标测量机的动态误差分析实验及结果
福州众印网 2006/8/4 10:54:00 来源:转载
三坐标测量机的静态或准静态误差主要由几何误差、构件有限刚度造成的误差、热误差3部分构成。往往采取误差修正的方法来减小静态或准静态误差。
除了静态或准静态误差外,三坐标测量机测量结果的精度还受到动态误差的影响。测量机速度的加快使动态误差对测量结果的影响更大。
随着三坐标测量机的动态误差对测量结果的影响越来越大,对三坐标测量机动态误差的研究也越来越受到人们的重视。动态误差主要是由三坐标测量机的结构特性,如质量的分布、构件刚度、阻尼特性、控制及干扰力所决定的,由各构件绕气浮导轨连接处的偏转和各运动构件本身的弯曲变形造成的。当测量速度较低时,这一误差很小,可以忽略不计。当测量速度较高时,尤其在高速扫描测量中,这一误差对测量结果影响较大。
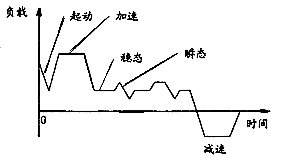
图1 负载变化过程
三坐标测量机运行过程中的典型负载变化情况见图1。
在对动态误差的实验研究中,往往测量各构件绕气浮导轨连接处的偏转角误差是比较容易的。各构件的动态偏转误差综合起来,成为测头位置处的动态位移误差。为估计这一误差的大小,Weekers等提出了一种运动学模型。由于三坐标测量机种类的多样性,模型往往不具有普遍性。本文针对一种三坐标测量机具体结构,进行了动态偏转角误差的测量,并推导出由动态偏转误差得到测头处的动态位移误差的方法。
理论分析
实验研究用测量机的结构见图2。横梁带动x-滑架及测头沿y方向运动,x-滑架在横梁上沿
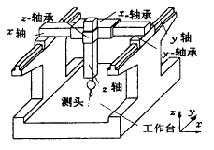
图2 测量机结构
x向移动,安装在滑架上的z轴带动测头沿z向移动。所有的导轨都是气浮导轨。其中在横梁的左右两端分别有对称的x向气浮导轨。在高速运动过程中,横梁本身、x-滑架及z轴的分布质量作用在横梁上,带来了附加的惯性力,使横梁相对于气浮导轨处产生偏转,并使横梁产生动态弯曲,所有这些偏转都将造成动态误差。
横梁的具体结构见图3。采用的坐标轴系为机器坐标系。A和B为气浮导轨连接处。设A点到x-滑架之间的距离为a,B点到x-滑架之间的距离为b。由x-滑架和z轴的质量带来的集中惯性力为P,由横梁的分布质量带来的均布惯性力载荷为q。
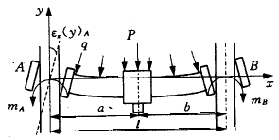
图3 横梁结构
在高速测量中,由于分布质量产生的惯性力将使横梁发生弯曲变形,而A、B的气浮导轨也具有一定的刚度,使x-滑架相对于导轨也产生一定的偏转。这样,在A、B将有附加的力矩mA、mB作用,横梁发生的是复杂变形。
由于三坐标测量机具体结构和运动的复杂性,在运动过程中的惯性力的大小是很难确切知道的,所以要通过其它的途径来解决这一问题。当横梁沿y轴运动时,动态偏转误差是绕z轴的偏转角,可以用εz(y)来表示。从理论上可以证明,在气浮导轨力矩刚度和横梁弯曲刚度已知的情况下,只要测量出气浮导轨滑架A、B两点的偏转角误差,就可以得到测头位置处的动态位移误差。
设在A、B点测得的动态偏转角分别为εz(y)A、εz(y)B,则
(1)
设横梁的弹性模量为E,惯性矩为I,则式(1)可以写为
(2)
设气浮导轨的力矩刚度为Kair,则
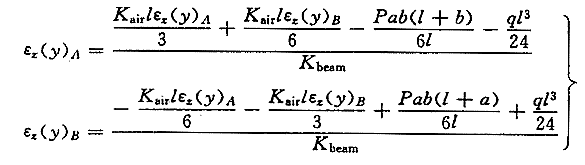
令Kbeam=EI,则式(2)可写为
(3)
由式(3)可以解出
(4)
(5)
式中,λ=(1+a)/(b-a)。 设测头位置处的动态位移误差为δy(y),则
(6)
将式(6)中各分量分别求出,得
(7)
(8)
(9)
(10)
从以上可以看出,当a和b的值比较接近时,(a-b)→0。用式(7)~式(10)得到的结果将有较大的不准确性。为解决这一问题,我们除测量出气浮导轨A、B两点的偏转角误差εz(y)A、εz(y)B外,另外测量测头位置处的偏转角误差εz(y)P。对于εz(y)P,有
(11)
式中,
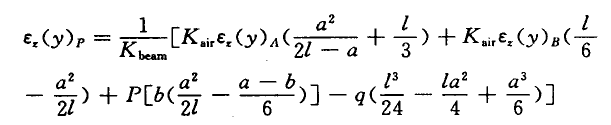
代入式(11)并考虑到mA=Kairεz(y)A和mB=Kairεz(y)B,有
(12)
将式(12)与式(3)联立,即可解出P和q。测头位置处的动态位移误差为δy(y)可用与式(7)~式(10)类似的方法得出。
实验过程及结果
在实验中,往往测量各构件绕气浮导轨连接处的偏转角误差是比较容易而且可行的。各构件的动态偏转误差综合起来,成为测头位置处的动态位移误差。测量各构件绕气浮导轨连接处的偏转角误差有很多方法,例如用激光干涉仪就可以准确地得到测量结果。但是激光干涉仪的测量结果受环境参数影响较大,对使用环境要求较高。在实际中,往往希望用较简单的方法来完成测量任务。为达到这一目的,我们在所研究的三坐标测量机上用其它方法进行了实验,采用的仪器是微位移传感器。实验中实际应用的是电感测微仪。
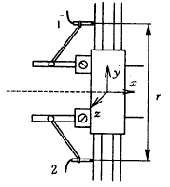
图4
以测量A点绕z轴的偏转角εz(y)A为例(见图4),2个经过标定的电感测微仪测头分别布置在1点和2点并垂直于y向导轨面。设在1点的电感测微仪的测量值为d1,在2点的电感测微仪的测量值为d2,1、2两点间沿x轴方向上的距离为L,则A点绕z轴的偏转角εz(y)A为
(13)
其它各角度误差可用类似的方法测出。εz(y)A测量结果见图5a。此时,测量机的速度为100 mm/s,加速度为100 mm/s2。
在测量过程中,我们发现导轨面的平面度对测量结果的准确性有很大的影响。为了消除这一误差因素,我们对A点绕z轴的偏转角εz(y)A进行了准静态测量。这时测量机的速度为10 mm/s,加速度为10 mm/s2。测量结果见图5b。
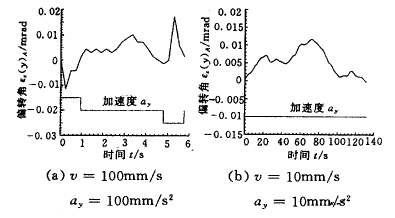
图5 测量结果
对比图5a和图5b的结果,我们可以看出,起动和减速阶段的惯性力造成了滑架的偏转。这一偏转量将导致测头位置处的位移误差。同样,由于导轨面的平面度也可导致滑架的偏转,从而引起测头位置处的位移误差。在本实验中,由于导轨面的平面度导致滑架的最大偏转为0.012 mrad,最大动态偏转误差为0.018 mrad。
气浮导轨刚度测量
可以看出,气浮导轨仍然是刚度较差的环节,其主要原因是气膜刚度较差。在实际的研究过程中,为了了解气浮导轨的刚度,往往采取直接测量的方法。目前,关于气体轴承刚度的实验研究,仍停留在静态测试阶段。三坐标测量机在实际应用中,速度是有一定限制的。即使在高速运动过程中(v=1000 mm/s),速度与音速相比仍然比较低,所以可以用静态刚度来代替这里的动态刚度。
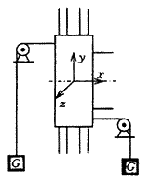
图6 测量装置
(14)
结论
三坐标测量机的动态误差主要是由各构件绕气浮导轨连接处的偏转和各运动构件本身的弯曲变形造成的。当测量速度较低时,这一误差往往很小,可以忽略不计。当测量速度较高时,尤其在高速扫描测量中,这一误差对测量结果影响较大。在对动态误差的实验研究中,往往测量各构件绕气浮导轨连接处的偏转角误差是比较容易而且可行的。各构件的动态偏转误差综合起来,成为测头位置处的动态位移误标测量机坐构,得到动的具体结差。因此,要针对三态偏转误差和测头处的动态位移误差的转换关系。运用本文提出的方法,可以方便地估计三坐标测量机动态误差的大小。在三坐标测量机的设计和测量方案的优化中都有很大作用。
本文标题:三坐标测量机的动态误差分析实验及结果
福州印刷.福州印刷网.福州印刷厂.福州众印网.宣传册印刷.宣传单印刷.包装盒印刷.手提袋印刷.印务公司.光盘印刷.中秋月饼盒包装印刷厂.企业画册印刷.不干胶印刷.无纺布袋印刷
福州印刷、福州印刷网fzysw.com福州专业的纸品印刷厂、福州众印网是超赞的印刷超市
|